熟料生料入窑磨粉压饼

精细优化操作参数 提高熟料产质量-水泥网
2011年8月1日 通过强化窑系统精细化管理,优化工艺操作参数调整等措施,回转窑产量由5300—5450 t/d提高到5600—5700 t/d,2010年上半年共生产熟料93万多吨,超额完成集 2014年6月3日 水泥窑由于生料分解要消耗大量的能量,为了减轻窑的负荷将分解功能移出窑外,专门设置了分解效率比窑更高的分解炉,由此形成了窑外分解窑。 那么,水泥磨 贾华平:对水泥生产粉磨工艺的技术展望-水泥网2017年3月10日 2水泥生产流程 典型水泥熟料生产线的工艺流程 1)石灰山矿山 概念 水泥主要原材料石灰石通过爆破矿山所得。 石灰石通过工具运输走以供破碎之用。 控制单元 破碎机、输送设备、收尘设备、长皮带。 2)石 几张图轻松了解水泥行业生产工艺和控制流程 - 知乎

水泥预分解窑工艺装备技术-水泥网
2005年1月20日 水泥生产过程中,产品质量控制的三个重要环节是:入窑生料质量和喂料稳定性,熟料率值和矿物成分设计值的合理性与熟料煅烧状况,以及水泥的粉磨细度、颗 2022年12月3日 (5)在生料入库斜槽尾部安装回转卸料阀+下料溜槽,使之与入窑提升机主斜槽连接,保证生料直接运输到入窑提升机。 同时在原有生料回灰仓底部新增一台罗茨 出磨生料直接入窑生产的实践出磨生料直接入窑生产的实践-【总页数】2页(P59-60)【作 者】张占龙; ... 1.高硅灰岩用于立磨的试验研究与生产实践——5 000 t/d生产线生料磨选型与使用2.配置辊压机生料终粉磨 出磨生料直接入窑生产的实践_百度文库

辊压机生料终粉磨运用之调研分析-水泥网
2014年7月14日 辊压机终粉磨技术起源于亚东花莲公司。 花莲公司原设计为辊压机加管磨,为了挖掘辊压机的节电优势,在停管磨的情况下,进行了辊压机单独粉磨试验,取得 2022年12月1日 亲,你好!. 好开心为您服务!. 出磨生料和入窑生料的区别:因为新型干法窑的悬浮预热器内风速很大,由一级筒进入预热器的生料粉在下落过程中与上升气流混 出磨生料和入窑生料有什么区别 - 百度知道2009年4月21日 石渣 熟料 水泥 窑尾 压滤机 生料 温度 预热器 滤饼 系统标签: 电石 熟料 配料 水泥 工艺 生产)水解后产生的沉淀物(工业废渣),主要成分为Ca(OH)(电石渣)每吨电石水解后约可产生1.15吨电石渣(干料),电石渣的堆放不仅占用大量的土地,而且因 ...电石渣配料生产水泥熟料新工艺的开发与应用 - 豆丁网

水泥的工业生产方法 - 百家号
王摩尔Kt 2022-09-27 22:41. 水泥的工业生产是以石灰石和粘土为主要原料,经破碎、配料、磨细制成生料,然后喂入水泥窑中煅烧成熟料,再将熟料加适量石膏(有时还掺加混合材料或外加剂)磨细而成。. 一、水泥的生产方法. 水泥生产随生料制备方法不同,可分为干 ...2018年11月29日 水泥生料在窑内的煅烧过程,虽方法各异,但都要经历干燥、预热、分解、熟料烧成及冷却等几个阶段。其中,熟料烧成是水泥生产的关键,必须有足够的时间,以保证水泥熟料的质量。 4、水泥熟料矿物组成 硅酸盐水泥的主要熟料矿物的名称和含量范围如下:土木工程材料 - jlu.cn2020年9月24日 水泥生产方法 水泥的生产工艺简单讲便是两磨一烧,即原料要经过采掘、破碎、磨细和混匀制成生料,生料经1450~C的高温烧成熟料,熟料再经破碎,与石膏或其他混合材一起磨细成为水泥。由于生料制备有干湿之别,所以将生产方法分为湿法,半干法或半湿法,干法3种。水泥厂生产流程及主要设备_江苏鹏飞集团股份有限公司官网 ...

生产水泥的工艺方式介绍,制备水泥的粉磨工艺流程? - 知乎
2023年2月9日 但也有将生料粉参加适量水制成生料球,送入立波尔窑内煅烧成熟料的办法,称之为半干法,仍属干法消费之一种。2、湿法消费工艺流程。将原料加水粉磨成生料浆后,喂入湿法窑煅烧成熟料的办法。也有将湿法制备的生料浆脱水后,制成生料块入窑煅烧成熟料水泥熟料以石灰石和粘土、铁质原料为主要原料,按适当比例配制成生料,烧至部分或全部熔融,并经冷却而获得的半成品。在水泥工业中,最常用的硅酸盐水泥熟料主要化学成分为氧化钙、二氧化硅和少量的氧化铝和氧化铁。主要矿物组成为硅酸三钙、硅酸二钙、铝酸三钙和铁铝酸四钙。硅酸盐 ...水泥熟料_百度百科2017年3月15日 二线投料初期,原材料碱含量高、结晶硅含量高导致出窑熟料 质量较差,突出表现在早期强度低,熟料标准稠度用水量高。 水泥网首页 ... 量基本不变的情况下,调整头尾煤比例(12.4:15.2),增加头煤量,二次风温控制>1150℃,生料入窑分解率 ...复杂有害成分对熟料煅烧的影响及优化措施-水泥网

流程图——水泥厂主要生产工艺流程 - 豆丁网
2021年1月4日 水泥厂主要生产工艺流程水泥生产过程主要分为三个阶段,即生料制备、熟料烧成和水泥粉磨(俗称“两磨一烧”)。其生产工艺总流程示意见图3-1。采用五级旋风预热及窑外分解的新型干法水泥的生产工艺流程说明如下:(1)石灰石破碎及储存由自备汽车从矿山运来的石灰石经生产能力为500-600t/h的 ...2011年8月1日 1.4.2 入窑生料三率值波动较大 回转窑煅烧强调“五稳保一稳”,入窑成份的稳定在五稳中占相当大的比重。以前我们没有重视对生料均化库底六个卸料区的管理,致使入窑物料均化效果较差,入窑三率值波动较大,窑况不稳,影响熟料产质量的提高。精细优化操作参数 提高熟料产质量-水泥网2022年9月13日 就目前水泥粉磨工艺流程而言,有以下几种:即管磨机(开路或闭路)粉磨系统、立磨粉磨系统、筒辊磨粉磨系统及辊压机终粉磨系统等。粉磨过程电耗要占水泥总电耗的70%以上,粉磨工艺的选择与应用直接影响水泥的产量、质量及生产成本,在水泥制备中占有举足轻重的地位。水泥粉磨工艺发展趋势及改造要点
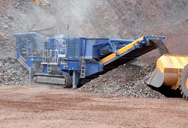
水泥的工业生产方法_的生产_生料_干法
2023年1月9日 水泥生产随生料制备方法不同,可分为干法 (包括半干法)与湿法 (包括半湿法)两种。. ⒈ 干法生产。. 将原料同时烘干并粉磨,或先烘干经粉磨成生料粉后喂入干法窑内煅烧成熟料的方法。. 但也有将生料粉加入适量水制成生料球,送入立波尔窑内煅烧成熟料的 ...2014年7月14日 在3台立波尔窑改为2 500 t/d熟料线后,生料制备系统仍延用原为立波尔窑配套的4台Φ3.2 m×8.5 m中卸烘干生料磨,能力为4×50 t/h,系统粉磨电耗为28 kW•h/t左右 ;而且烘干用热风炉,烘干煤耗约8~10 kg/t。为节电和节煤计,于2008年上了一套辊压机生 辊压机生料终粉磨运用之调研分析-水泥网2021年6月17日 氧化铝熟料窑生产工艺新的煅烧铝矾土熟料的生产工艺流程如下:原料进厂→库→破碎→粉磨→脱硅→湿法均化→过压滤→练泥→挤出成型→烘干→煅烧→破碎→出厂成品。. 1、矿浆制备 (拜耳法氧化铝工 氧化铝熟料窑生产工艺 - 知乎
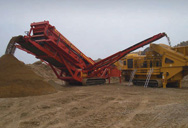
电石渣100%代替石灰石生产熟料的优化改进措施
2017年6月15日 采用100%电石渣代替石灰石生产熟料,某些工艺操作参数与石灰石配料有所不同,在操作上应时刻掌握入窑生料的变化情况,用风是关键,用煤要掌握窑头与窑尾的比例,化验室在配料中要根据电石渣的成分和氯离子含量选用与匹配其他原料,优化配料方 2023年10月7日 熟料煅烧阶段:将制备好的生料送入水泥窑内煅烧至部分熔融,得到以硅酸钙为主要矿物成分的水泥熟料。 水泥粉磨阶段: 将熟料磨细,并在磨细过程中加入适量的石膏和一定量的混合材料共同磨细成水泥,采用袋装和散装两种方式进行装运。易碳大咖说 水泥产品碳足迹分布与减碳路径分析 - 知乎水泥工艺学第五章水泥熟料的煅烧. f一、回转窑内物料流速和窑的煅烧特点. 1、流速 在回转窑的斜度和转速不变的情况下,烧成带最慢、 碳 酸钙分解带最快。. 2、煅烧特点 (1)保持烧成带一定的温度和足够的停留时间。. (2)CaCO3的分解效率是回转窑熟料煅烧 ...水泥工艺学第五章水泥熟料的煅烧_百度文库
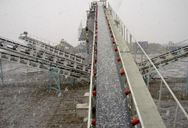
硅酸盐水泥国家标准及其生产_百度文库
凡是由硅酸盐水泥熟料,600^15%混合材料、适量石膏磨细制成的水硬性胶凝材料,称为普通硅酸盐水泥(简称普通水泥),代号P O. 掺活性混合材料时,最大掺入量不得超过15%,其中允许用不超过水泥质量5%的窑灰或不超过水泥质量10%的非活性混合材料来 ...2021年3月20日 水泥厂磨粉加工流程. 水泥生产过程是一个工艺设计复杂的流程,只有对每一个环节有着全面的了解,才能有效地提升生产效率,保证水泥生产质量。. 提到水泥的生产都会说到“两磨一烧”,它们即是:生料制备、熟料煅烧、水泥粉磨。. 通常来讲,水泥工业 ...水泥厂磨粉加工流程 - 知乎2016年3月23日 毕业设计说明书日产2500吨水泥熟料干法水泥厂设计学院(部):材料工程学院专业班级:材料工程学生姓名:指导教师:20**工艺流程水泥生产过程可概括为生料制备、熟料煅烧、水泥粉磨。. 生产方法依生料制备方法不同分为干法和湿法。. 湿法生产产量低 ...日产2500吨水泥熟料干法水泥厂 设计 - 豆丁网
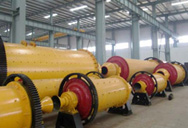
贾华平:对水泥生产粉磨工艺的技术展望-水泥网
2014年6月3日 实验采用四川某厂硅酸盐水泥熟料,在熟料中加入3%石膏后分成两部分,一部分进φ500×500球磨,磨细成球磨水泥;另一部分经辊压机挤压成料饼(其中包含部分合格细粉),其中粗粉在实验室装入模具挤压至合格。